Sketchup Cut Hole In Curved Surface

Use the quicklinks at right to jump to specific topics.

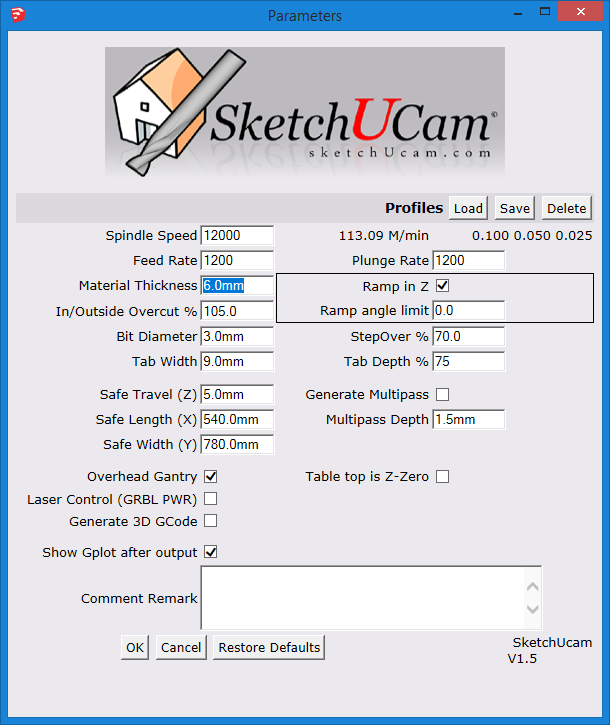
Enter Phlatboyz Parameters to set:
[spindle speed,
feed rate,
plunge rate, (also used for ramp moves)
material thickness,
ramping options,
Inside/outside overcut%,
bit diameter, Stepover%,
tab width, tab depth factor,
Multipass options,
the safe cutting area size and comment text]
which will appear in the generated g-code.
All g-code output uses the safe cutting area's local origin(the bottom left corner) or the origin set by the offset tool and only edges entirely within the safe cutting area will generate g-code.
You can also SELECT cut lines within the safe area and only those selected edges will cut.
This will allow designs requiring multiple sheets to be contained within one SketchUp file and the cut codes processed as one sheet at a time for separate g-code files for each sheet. The safe area defaults to Sketchup's origin, unless placed elsewhere using the Safe Area Tool.
Also, there are check boxes for additional options:- "Generate Multipass" - for cutting hard materials, where you want to limit the depth of cut by cutting multiple thin layers.
- "Overhead Gantry".
The original 2 Phlatprinters cut from the bottom with a reversed Y axis. Use this option if you have a Phlatprinter3 or your cnc machine has an overhead gantry. This will reverse the direction of the Inside and Outside cuts.
New in V1.5: This setting replaces the old Tools menu settings for pockets and plunge holes. Now pockets and plunge holes will cut in the direction set by this option.
Note: In older files the pocket direction can sometimes not be determined and this setting will be ignored. In this case, remove and replace the pocket cut to get the correct direction of cut.When this option is:
See the Options Menu help for setting this as a default
Ticked: outside cuts will cut anticlockwise
(a conventional cut)
Unticked: outside cuts will cut clockwise
(a climb cut)
- "Table top is Z-zero" - tick this to use the table surface as the zero reference point for Z.
If this is OFF then the top of the material is the Z zero reference point.
- SFM display
This line displays, from left to right- The SFM calculated from the RPM and tool diameter, this is the speed at which the cutting edge goes past the material.
- The feed per tooth for a single tooth cutter. Calculated from the feedrate and the RPM.
- The feed per tooth for a 2 flute cutter.
- The feed per tooth for a 4 flute cutter.
- "Laser Control" [checkbox] New in 1.4a and updated in 1.4c
Tick the Laser Control box on the parameters dialog and G-code will be output suitable for laser cutting on a machine that uses spindle commands to control the laser.
The current control scheme replaces all Z movements (start and end of cuts) with M03/M04 and M05 spindle motor on/off commands.
The M03/4 is combined with an S word giving PWM control of the laser power.
This value is set to the cut depth percentage of the current 'Spindle speed' set in the parameters dialog.
For example, if your controller accepts 10000rpm as the maximum spinde speed, then set that in the parameters dialog.
Now, for a 100% deep centerline cut, laser on command will be- M03 S10000
- M03 S5000
If you are using GRBL 0.9 (and later) the default max spindle speed is 1000.
If your laser only supports full on and full off and cannot use PWM, then always use 100% deep cuts (and a correctly set maximum spindle speed as well) and the spindle control output will always be either on or off.
DO NOT select 'ramping' nor 'Gen3D' when Laser Control is desired.
Ramping and Gen3D will be turned off automatically.
Multipass can be used to get cleaner edges in some materials. Experiment for yourself!Multipass in laser mode will use a constant power level.
Plunge holes: there are 2 modes: GRBL mode will draw a 0.2mm diam circle, not GRBL mode will create a dot at the center of the hole. The length of the delay at this dot can be adjusted via the Hole Feature Options dialog.
Large holes will draw a circle of the defined diameter (with no allowance for beam width).The display of the parameters dialog will change according to the laser mode selected:
- If GRBL mode is 'false'
-
- If GRLB mode is 'true' and GRBL power mode is 'false'
-
- If GRLB mode is 'true' and GRBL power mode is 'true'
-
Summary:
- works with both Z-Zero options
- No Z motion will be in the Gcode output
- M03 or M4(spindle on) and M05 (spindle off) will control the laser
- The S word will be set to control the brightness via PWM spindle control.
- The S word is set to a proportion of the current spindle speed, according to the depth of the cut.
Thus a 50% deep centerline cut will set the S word to 50% of the spindle speed. - If your laser needs on/off control, then simply always use 100% deep cuts and max spindle speed (1000rpm for default GRBL settings). With these settings the PWM control will effectively only turn hard on and hard off. (also leave GRBL Power mode = false in hole feature options!)
- See Hole Feature Options for an explanation of how the laser setting interacts with GRBL's laser modes.
- Use normal tabs, not V-tabs. Only half of a Vtab will be 'cut' at the defined power.
You can read more about GRBL's laser mode in the GRBL documentation
Note: When you press "OK", these settings will be saved as attributes to your sketchup model. So each sketchup file will retain their individual settings.
Profiles
New in 1.1c is the ability to save and restore tool profiles. This allows you to quickly restore a tool setup that relates to a type of material or operation. For example one might store the settings for a drilling operation with multipass on, low feed speeds etc. For a foam milling tool one can store high feed speeds, not multipass and so on.
Clicking the 'Save' button will produce a prompt for a profile name. Profile names must not have spaces or punctuation in them. The following settings will be saved
|
|
Note the material thickness is deliberately not saved. The concept of the profile is to save a tool setup for a specific type of material rather than a size of material.
Clicking the 'Load' button will bring up a prompt box showing the currently available profiles. Select one and click 'Ok'.
After a load, the comment parameter will read "Loaded profile NAME" where NAME is the name of the profile.
The 'Delete' button will allow you to select a profile and delete it.
For those using the compatibility menu (on Mac or Linux) the profile functions are available on the Tools|Phlatboyz menu.
Also on that menu us the Options Summary entry. This will display your current settings for a number of global options settable in the Options menu. Yes, we know it is misnamed 'Validity Check', that is a Sketchup default we cannot change :-) Please see the Options help.
See also: Tool Change
As of V1.4 you will prompted for tool information when you save a tool profile. IF you enter tool information, this will automatically enable tool code output when you load the profile.
Some points to note:
- Inside/Outside overcut%
- This value is used as a multiplier on the material thickness. The Phlatprinter is designed to cut through sheet material so normal cuts must go deeper than the material thickness. This is normally about 140%, ie through the material and 40% out the other side to account for wavy dollar tree blue foam. If you are using an overhead gantry and do not want to cut into your spoil board then set this value to 100% and zero your toolbit end accurately.
- Plunge rate:
- used for vertical down moves of the Z axis. Set this (much) lower than the feed rate for hard materials.
This is also used for ramping moves, and while it can be much faster than plunging, in harder materials it should be slower than the normal cut feed rate. - Table top is Z-Zero
- If this is checked then Z zero level is on the table top, if unchecked, Z-Zero is on the top of the material (the default).
- Ramp in Z more HOWTO help here
- If this is unchecked Z will be plunged, if it is checked, Z will ramp into the workpiece along the first segment of the cut (yes, even arcs will ramp, some controllers cannot do helical arcs so check this before a big job).
The angle set in 'Ramp angle limit' will be used.
If this is '0' then there is no limit, otherwise you can enter a value from 1 to 45 degrees.Be aware that this cut may be very short (and therefore a steep angle if not limited) .
and you may need to adjust cut order to get the cut to start on a longer segment.The Plunge Feed Rate will be used for ramp moves.
If the segment is longer than 5 x bitdiameter then the ramp will be limited to a length of 5 x diameter on straight segments. Arcs will use the arc length.
If a cutline has no segments that are longer than half the bit diameter then a plunge will be generated instead of a ramping move. The cut start point optimizer will try to find a long enough segment but if it fails then a plunge will be generated. If you have comments turned on, you will see a message like
(ramplimit end, translated to plunge)
warning you that the G-code will plunge cut.If your tool cannot plunge cut then it is critical that you check the Gcode for such messages before using the G-code.
Note that ramping will affect plunge holes like this:- With depth first option selected 'Tools|Phlatboyz|Options|Hole Feature Options'
-
dia = tooldia tooldiam < dia <= 2D dia > 2D Stepover% < 50% Will Plunge no plunge, 2 helical bores no plunge, 2 or more helical bores stepover% > 50% Will Plunge no plunge, single helical bore no plunge, 2 or more helical bores
- With diameter first option selected 'Tools|Phlatboyz|Options|Hole Feature Options'
-
dia = tooldia tooldiam < dia <= 2D dia > 2D stepover% < 50% Will Plunge no plunge, 2 helical bores no plunge, 1 helical bore, then spiral out to diam stepover% > 50% Will Plunge no plunge, single helical bore no plunge, 1 helical bore, then spiral out to diam
If you are making holes equal to the bit diameter in hard materials then you should use a real drill bit and do a seperate drilling cycle.
- Ramp angle limit
- If this is 0 then there is no limit on the ramp angle. This means that short segments will be ramped almost vertically. If set to an angle from 1 to 45 the ramp angle will be limited to this value, ie it might be less for a long segments, but will never be more. Multiple ramp moves will be generated to achieve this angle, while the total number of ramp moves will be rounded to always be an even number, ensuring that the limiting angle is not exceeded.
- Step Over %
- This percentage is used by the by the Pocket Tool and Plunge Hole tool (and 3D code generator) to determine how much of the bit diameter to overlap each cut pass.
Tool manufacturers recommend using 1-30% or 70 to 100%, but not 30-70% as this range increases tool wear. - Tab width
- Half the bit diameter will be removed from each end of the tab. Thus a tab width equal or less than the bit diameter will not leave a useful tab at all.
- Tab Depth %
- The percentage of the material thickness to cut away when doing tabs. Thus 75% will cut away 75% of the material leaving 25% behind. Note that the bit will remove a little extra material at the top of the V, the bigger the bit the more will be removed. This means that the remaining material will be a bit thinner than expected.
- Generate 3D Gcode
- Tick this if you need to generate a cut over the top of a 3D object. (ie not the usual flat drawing)
Please read the 3D help! and be aware that other packages like pyCAM do a much better job of 3D than we do at the moment. - Only select 'Generate 3D Code' for an actual 3D model. If selected for a plain flat drawing, Sketchup Will Stop Responding
- Show G-code after output
- Ticking this will cause Gplot to display the G-code directly after generating it. The Gplot program will open after you click 'Ok' to confirm the file save. Note that Sketchup 2013 onward requires you to click on the drawing, or select a new tool, before the G-code program will be displayed.

If the preview shows the outside cut on the wrong side, reverse the face, outside cut must only be used on the outside of a polygon
Use the
["End" key] if the tool locks onto the wrong adjacent face. You won't need this feature, if you hover over faces instead of edges.Note: Reversing the face (Edit/Face/Reverse Faces) prior to using the Outside Cut Tool will cause the cut direction to be reversed. This works the same as the Inside Cut Tool. This may have unintended side effects on arcs!

If the preview shows the inside cut on the wrong side, reverse the face.
Use the
["End" key] if the tool locks onto the wrong adjacent face. You won't need this feature, if you hover over faces instead of edges.Note: Reversing the face (Edit/Face/Reverse Faces) prior to using the Inside Cut Tool will cause the cut direction to be reversed. In milling, the rotation of the bit, counter clockwise or clockwise, determines which edge of the design will be left rough. Normally, in SketchUp, you would leave the default grey side facing up for all faces, before you assign cut lines. Otherwise, if the face is reversed (white), and a cut line is assigned whether inside or outside, the rough edge will be on the part and not the waste. So, in short, make sure that the grey side is facing up and SketchUcam will cut your part file in the right direction leaving a nice clean edge on the part.

This tool uses the tab width and tab depth factors which are defined in the Parameters dialog. Use that dialog to define the tab tool parameters prior to using the tool; changing the values in the Parameters dialog will not affect tabs that have already been placed.
Use the
["End" key], to toggle from standard Tabs to V-Tabs. V describes the angled tabs vs the standard rectangular tabs. The cursor will change from a T to V to show the current mode.Use the
["Home" key], to toggle Bold Tab viewing mode off/on. When the tab tool is active, this feature makes the tabs easy to see. Turn it off, if sketchup slows down when using the tab tool.Note: A feature of the Tab Tool is the ability to 'draw' tabs to any width you desire always starting with the default width. For example, if the tabs placed along a curve are too small, you can hold the left mouse button down and draw then in wider. The tab depth will remain the same as defined in the parameters dialogue.
Note: The tab tool has click/drag functionality, for multiple tabs or extending tab width.

It automatically selects a single edge. Press the
["Shift" key], if you want all connected edges.Use the
["End" key] to toggle between short and wide mode. When hovering over an edge, the short mode shows a pink color preview. Wide mode shows a darker red/purple preview color. Short and Wide mode status is also shown on the bottom status text. The default short mode will shorten both ends of the edge by a small amount. The main reason is to break contact and stop the possible creation of an extra face and loop, which could confuse SketchUcam. Wide mode will act normally and not offer this protection. But you can use wide mode, if say you want a connected chain of edges.Use the
["Left Arrow"]["Right Arrow"] keys to scroll through the preset depths: [25%, 50%, 75% & 100%]. This will result in the cut depth, as a percentage of the material thickness. You can see the current depth factor in the VCB (lower right hand corner in SketchUp).Use the ["Down" key] to set the depth back to the default of 50%.
Note: You can type custom depth values into the VCB, using your keyboard. The value is not accepted, until the "Enter" key is pressed. Then the % suffix will appear with the VCB value, which indicates the value is now set. Max value allowed is 140%.

The plunge tool creates a circle with a brown radius line extending from the center to the outside diameter. The diameter of the circle is determined by the Phlatboyz "Bit Diameter" parameter.
The plunge tool allows the generation of G-code required to plunge the bit at the depth indicated in the "Material Thickness" Parameters dialog.
OR
You can set the percentage depth before you click. This hole will then be that percentage of the material thickness in depth. You will need to set the depth for every hole.
AND
You can hold down the SHIFT key when clicking, and you will be prompted for a diameter.
The hole will then be spiral bored to that diameter.
This is a relatively slow way to cut a hole so holes that are greater than 3 times the diameter of the bit should rather be a circle with an inside cut to remove the waste. However, if you are cutting soft material (large or no multipass) and using the 'diameter first' cut strategy, the cut will be quite quick.
Feedrate in the helix will be the normal rate set for cuts.
Downfeed will be limited to either
- half the bit diameter per revolution
- the multipass depth if multipass is on.
- the calculated Z feed if ramp angle is set, in order to achieve the correct helix angle.
New in V1.2a : Plunge holes are automatically grouped.
This (mostly) prevents underlying geometry from interfering with G-code generation.
Only an underlying horizontal line will interfere but in this case it is very easy to delete the part that overlaps the colored 'hole' line, or, you can group the underlying line before placing the holes.
Ordinary holes have no group name while enlarged holes are named with the diameter and depth.
For example a plain 8mm hole will be named "_diam_8.0mm" and a depth restricted 9mm hole will be "_diam_9.0mm_depth_76.0".
This implies that holes will be cut in group order so don't forget to set the order with the Group Reorder tool if you need to.
Do many holes with large diameter
New in V1.4 is the ability to lock the large diameter setting so that you can easily create many holes with the same large diameter.
Tap the HOME key to set 'LARGE LOCK' on and be prompted for a hole diameter that will persist until you select another tool or tap HOME again.
![]() |
![]() |
Holes in a grid pattern
Hold down ALT or CTRL key to be prompted for a grid pattern of holes to drill. They will all use the same parameters. Note that the Horiz and Vert Count refer to the number of holes. If you need to space a number of holes, say 7, along a length (say 52mm), then the spacing is calculated by
52/(7-1) = 52/6 = 8.666mm.
If either Horiz or Vert count are '1' then you get only 1 row or column of holes.
- Note that the various CNC controllers will perform this operation in different ways. LinuxCNC will do true spiral decending cuts, while other controllers might step down and do a circle with constant Z instead.
- The normal cut direction is anticlockwise giving a 'climbing cut'. On stiff machines this will give a superior surface finish. If your machine gives a bad finish in this and pocket cuts, please review the Use_pocket_CW and Use_plunge_CW settings in the Options menu section
- Depth first or Diameter first (new in 1.4)
Up to now holes have always been bored using a depth first strategy. ie for each stepover of the bit, it helical bored to final depth.
By setting the 'Use depth first or diam first' option to false, the 'spiral out' strategy will be used. This uses the following steps: (only for holes larger than 2 * bit_diameter!)- Helical bore the center hole to 2*bitdiameter
- Spiral out to desired diameter using either multipass depth layers, or a fuzzy calculated depth based on the bit diameter.

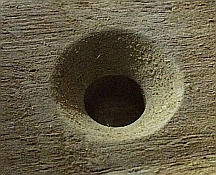
The example pictured at right was created using a 9mm straight flute bit. The hole is 12mm diameter, 15mm deep, and the countersink is 25mm diameter. The wood is unknown and resulted in fluffy edges, so what you see has been cleaned up by a few swipes with sandpaper.
When you click the icon to select this tool, you will see a dialog box as pictured at right.
This permits you to set the values you want for your CounterSINK/BORE holes.
These settings will be used for all future click events until you re-select the tool, or hold down SHIFT to be prompted for a hole diameter (countersink/bore diameter and angle or depth will stay the same).
The Countersink tool
The Countersink tool creates a grouped symbol of 2 circles with a blue radius line extending from the center to the outside diameter of the inner circle.
The inner circle is the current bit diameter, or the hole diameter given in the dialog, which must be greater than the bit diameter.
The outer circle is 8 sided, coloured blue, and represents the diameter given for the countersink portion of the hole. (yes, the countersink will be cut perfectly circular despite the octagonal symbol)
When setting the hole diameter, a diameter of 0.0 will use the current bit diameter.
The step down for the countersink portion is 0.25mm per layer, with the decrease in radius being calculated from the angle selected in the dialog.
Common angles are 82 and 90 degrees, with 100 or 120 degrees being used in thin sheet metal applications. Use the one that matches your screws! Angle is limited to >= 70 and < 180 degrees.
The CounterBORE tool
By selecting CounterBore from the first drop down list the tool will create counterbore operations, making a symbol as shown at right, showing the center hole diameter as for the countersink tool, and the outer diameter shown as a 9 sided figure in green. The radius indicator line will be green.The angle setting is ignored, and the 'Set Depth' setting is used for the depth of the counterbore. This is set using the current model units. Optionally set the 'Hole Diameter' to have a full depth hole that is bigger than the bit diameter. Set to 0 to have a plain bit diameter hole.
- Counterbore depth cannot be greater than the current Material Thickness.
- Hole Diameter cannot be larger than Countersink/bore diameter.
The hole depth is ALWAYS 'overcut%' deep, you cannot specify a shallower depth. This is because the countersink/bore portion has to have a central hole of at least bit_diameter to start from that is guaranteed to be deeper than the bottom end of the countersink or counterbore depth.
You can hold down the SHIFT key when clicking, and you will be prompted for a diameter. The hole will then be spiral bored to that diameter before the countersink/bore is created.
Hold down ALT or CTRL key to be prompted for a grid pattern of holes to drill. They will all use the same parameters.
Feedrate will be the normal rate set for cuts.Downfeed will be limited to either (and will use fuzzy calculation)
- Half the bit diameter per revolution.
- The multipass depth if multipass is on.
- Note that the various CNC controllers will perform this operation in different ways. LinuxCNC will do true spiral descending cuts, while other controllers might step down and do a circle with constant Z instead.
- While the hole boring part will obey the Use_plunge_CW setting, the countersink portion can only cut counterclockwise and always uses the 'spiral out' strategy.

It automatically selects all connected edges. Press the
["Shift" key], if you only want a single edge.Use the
["Left Arrow"]["Right Arrow"] keys to scroll through the preset depths: [25%, 50%, 75% & 100%]. This will result in the cut depth, as a percentage of the material thickness. You can see the current depth factor in the VCB (lower right hand corner in SketchUp).Use the ["Down" key] to set the depth back to the default of 50%.
Note: You can type custom depth values into the VCB, using your keyboard. The value is not accepted, until the "Enter" key is pressed. Then the % suffix will appear with the VCB value, which indicates the value is now set. Max value allowed is 140%.

A pocket is a shallow depression in the surface of the part.
As of V1.4c this tool has 2 modes:
- Default mode
- In this mode the tool can deal with simple convex polygon shapes.
- FLOOD mode
- This mode is for pocketing complex polygons that may have internal holes, however, processing takes much longer.
Default mode
This mode will add both a contour outline and the zigzag with one mouse click. The following control keys can be used:
- CTRL
- Hold down control to insert only the contour outline. This gives you the opportunity to check (and fix) the contour as it can generate odd shapes around sharp internal and external corners.
- SHIFT
- Hold down shift to insert only the zigzag line. You would use this after inserting the contour line.
- END
- Each press of the END key will toggle the direction of the zigzag lines from vertical to horizontal and back. This allows you to choose the direction that suites the shape, or that suites the machine dynamics.
- HOME
- Switch to FLOOD mode.
FLOOD mode
While this mode can deal with more complicated polygons, using it is also a bit more complicated so please note the following:
This is a 2 stage process, you will need to hold CTRL and insert the contours (left click), then point at the new face created and left click again (without CTRL) to insert the zigzags.
Fuzzy stepover is always used in FLOOD mode.
To activate FLOOD mode, press the HOME key. The status bar will change to indicate the mode.
- Normal mode status bar
-
- FLOOD mode status bar
-
The following control keys can be used:
- CTRL
- Hold down control to insert only the contour outline. This gives you the opportunity to check (and fix) the contour as it can generate odd shapes around sharp internal and external corners. In particular you need to check for overlaps between contours around internal shapes and the main outline.
- END
- Each press of the END key will toggle the direction of the zigzag lines from vertical to horizontal and back. This allows you to choose the direction that suites the shape, or that suites the machine dynamics.
- HOME
- Switch to default mode. Note that after inserting the zigzag, the tool will automatically switch to default mode.
for both modes
You can set the default zigzag direction in the Options menu
Note: You can type custom depth values into the VCB, using your keyboard (in addition to using the arrow keys to select a depth). The value is not accepted, until the "Enter" key is pressed. Then the % suffix will appear with the VCB value, which indicates the value is now set. Max value allowed is 99%.
Fuzzy stepover (new in V1.3a)
The pocket zigzag can use either the exact stepover% set in the parameters dialog, or it can use 'fuzzy stepover'.
Using the exact stepover may result in a gap at the end of the zigzag that is much larger than the stepover%, causing the final outline cut to remove a chunk of material that is near to bit diameter. This could break the bit in harder materials.
The option 'Use fuzzy pockets' defaults to ON since this results in a safer, optimal, zigzag spacing. You can change this setting on the Tools|Phlatboyz|Options|Features menu
The stepover is recalculated such that there is no remainder at the end of the zigzag, making the final cut the same width as the first cut. (This may vary for complex shapes, use a smaller stepover for complex shapes, and change zigzag direction to find the best fill).
The stepover is calculated as a SMALLER value if stepover% is less than 50%. It is calculated as a larger value if stepover% is LARGER than 50%. if stepover% is exactly 50% is uses that value. According to tool manufacturers using a 50% tool stepover will significantly shorten tool life so you should never use this anyway.
The offset from the bounding rectangle to the zigzag edges is calculated from the stepover% as follows:
stepover% < 75% offset = stepover% / 2 stepover% < 85% offset = stepover% / 3 stepover% <= 100% offset = stepover% / 4
This means that the offset is adjusted smaller as the stepover increases. This is done to prevent leaving large wedges for the final cut to handle, this happens especially on curved or sloped edges. Note that in FLOOD mode the zigzag will approach very close to the contour lines in places. This is normal.
MultiSelect pocketing (new in v1.4)
- If multiple faces are selected when the pocket tool is selected, all the faces will be pocketed
- All selected entities will be UNselected after this process
- If only one thing is selected, nothing is done, process is ignored
- Make sure you have the correct pocket parameters before doing the multiselect operation! (this works for FLOOD mode as well, select flood mode then select multiple faces, then when you select the pocket tool again it will zigzag all selected faces.)

Default is to erase all types of Phlatedges. This is the cursor that has no letters next to it.
Use the
["Left Arrow"]["Right Arrow"] keys, if you want to erase only one type of edge. It will cycle through and show in the VCB(lower right hand corner of SketchUp) which line type is currently assigned to the eraser. Also, each type has it's own unique cursor.Use the ["Down" key] to quickly go back to the default "erase All types".
Tab highlighting has been added to the eraser tool:
Use the
Note: The right click context menu will also allow you to erase ALL selected Phlatboyz edges.
Tip: Instead of deleting one item at a time, select many or all. Activate the eraser tool. And click the selected items. If any unwanted Phlatboyz edges still remain, then repeat.

G-code output will be generated only from designated Phlatboyz edges within this safe rectangle and will be relative to the safe origin (bottom left corner) unless moved using the 'Set 0,0 offset' tool.
If any cut edges are selected within the Safe Area, only those selected edges will generate Gcode. Use this when generating Gcode for large complicated drawings where a lot of lines are outside the Safe Area. By selecting the items within the Safe Area that you want cut, SketchUcam can ignore all other lines and therefore generate Gcode much faster.
Note: Even if the user doesn't use this tool to graphically define a safe area, the safe cutting area still exists and assumed to be at sketchup's origin unless it is moved using the default settings in the Options|Machine Options dialog.

Grouped cuts will be cut first, in the order they were grouped. However, in order to edit a group it has to be exploded. Grouping it again affects the cut order.
To reorder groups select this tool and then simply click on each group in the order you want them cut.
You can use the 'Tools|Phlatboyz|Groups Summary' menu item to see the current group ordering.

(However, it should still be within the Safe Area!)
- Select the tool
- Select the position for the 0,0 point (for example the center of the part)
- Select the tool
- Select the bottom left corner of the Safe Area

More information here
See also: Tool Change

The SketchUcam will calculate the optimal cut order. Or you can choose your own cut order. You do this by grouping your parts and they will be cut in the same order.
Note: The output g-code file has the extension .cnc but is simply a text file of X, Y, Z coordinates for the Phlatboyz machine to follow. Depending on your control software, this extension can be renamed to anything desired. To edit the g-code file, you can right click and open with a text editor of your choice. If you alter this file, your machine may do unexpected things, be very careful!



Known to not display on Linux under WINE, search for file help.html under the Sketchup Plugins folder within ~/.wine. Installing IE8 using 'winetricks ie8' may solve this.
Sketchup Cut Hole In Curved Surface
Source: https://swarfer.github.io/sketchucam/sketchucamtoolbar.html
Posted by: muhammadreepeemsess.blogspot.com
0 Response to "Sketchup Cut Hole In Curved Surface"
Post a Comment